Rieter’s Ri-Q-Tubes used in ring and compact-spinning machines are crucial to ensure smooth and reliable operation. Due to a special plastic blend material, the dimensional stability of the tubes remains the same throughout the lifetime. Hence, customers can expect a lifetime twice as long as that of conventional tubes.
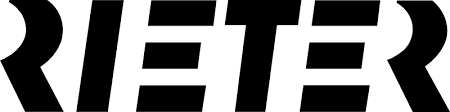
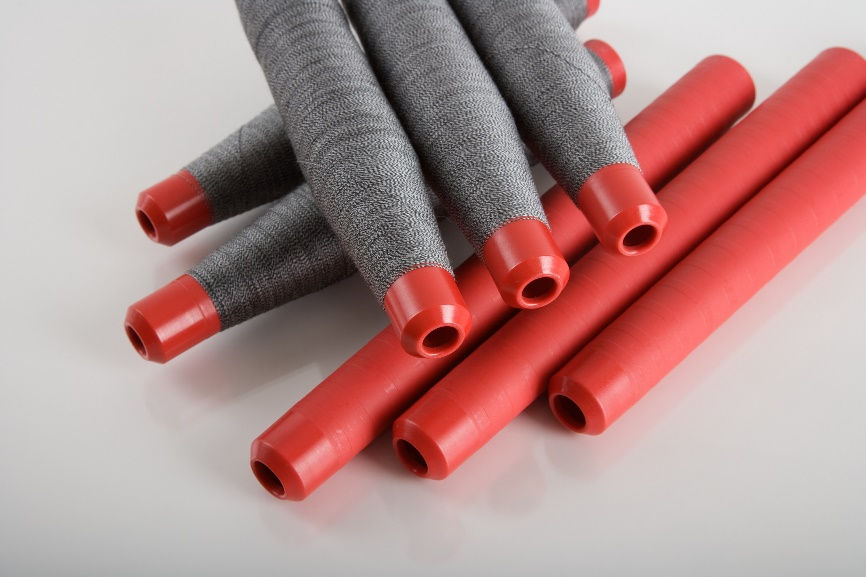

Customers all over the world have been relying on Rieter Ri-Q-Tubes for decades (Fig.1). “Our experience with Rieter tubes has been exceptional,” says Alluri Varun Varma, Business Development Executive of PVR Spinning and Weaving Ltd., India (Fig.2), adding: “Since their installation in 2014, they consistently deliver outstanding performance, surpassing the 10-year mark with ease.” The plastic tubes are an indispensable component used in the ring and compact-spinning machines for yarn packaging. The cop, a tube with yarn wound on it, goes through various stresses at each process. Initially, the tubes have continuous contact with spindles at high speed during cop build-up in the ring and compact-spinning machines. Then, the full cops are removed, and empty tubes are pressed on the spindle by the doffer arm during the doffing process. Later, the full cops are transferred to the winding machine Autoconer to unwind the yarn. The empty tubes are fed back to the ring and compact-spinning machine.
Long-term stability for high operating reliability
Rieter’s Ri-Q-Tubes have been specifically designed for the company’s ring and compact-spinning machines, which guarantee precision and longevity. The tubes are made up of a special plastic Polybutylene Terephthalate (PBTP) composition that supports higher spindle speeds. The material of the tube is unaffected by roughening of the inside surface, which can occur when the tubes run continuously. The special material properties avoid this effect and in addition the tubes are self-lubricated to make sure they slide down on the spindle easily.


Automated doffing reliability is determined by the perfect removal and insertion of the tubes on the spindles of the spinning machines. Tests with comparative measurements over 25 000 doffs clearly show that press-on force during doffing is much lower and consistent with Rieter Ri-Q-Tubes over the lifetime (Fig.3). The decisive factor is the doffer beam, which presses the empty tubes to the spindles at a constant force during every doffing operation over the entire length of the machine. If the tubes fail during this operation, the doffer beam can suffer damage, which interrupts doffing and reduces machine efficiency. Ri-Q-Tubes are highly reliable, ensuring smoother doffing operations and offering double the lifetime compared to conventional tubes. Alluri Varun Varma states: “The reliability and consistent presson force during doffing has been invaluable to the machine operations.”
Outstanding quality features
Rieter Ri-Q-Tubes are designed in conformity with the ISO 368 standard which specifies the dimensions and permissible total run-out of tubes used in the textile industry. The surface of the spinning tubes features special non-slip properties, which ensure optimum yarn take-up even at high spindle and winding speeds. The concentricity is maintained with a permanent quality control system during production enabling extremely high-dimensional stability of the tubes. This has a positive influence on the fit of the tube on the spindle. By running the spindles at higher speed, the tubes tend to rise. The better dimensional stability, or concentricity, of the Ri-Q-Tubes help to avoid this (Fig.4).
The concentricity combined with the self-lubrication property of the tube ensure the following benefits for customers:
• Minimum press-on force on the spindles during doffing,
• Longer lifetime of the tubes and the spindles,
• Increased durability of doffing parts and
• Uniform seating of the tubes on the spindles for proper cop build up.
Rieter offers a wide product range of Ri-Q-Tubes with tube lengths from 180 mm to 250 mm. They are available in various colors based on customer requirements for both manual and automatic removal of yarn residues. Specially formed gripper teeth inside the tip of the tube are available for elastic core-spun yarns or yarns with a strong tendency to snarl.
For further information, please contact:
Rieter Ltd.
Rieter Management AG
Media Relations
Relindis Wieser
Head Group Marketing & Communication
T +41 52 208 70 45
Σχόλια